Business
/ArcaMax
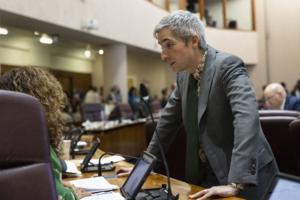
Chicago 'granny flats,' coach houses one step closer to citywide legalization with vote
CHICAGO — Aldermen advanced a measure that could legalize “granny flats” citywide with limited restrictions, a move advocates say will create more affordable housing.
The City Council’s Zoning Committee voted 13-7 to advance the additional dwelling unit ordinance. The result tees up a Wednesday vote by the full City Council, when ...Read more
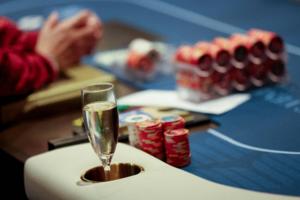
Big change coming for Las Vegas poker players at Strip casinos
A change in how, and where, poker players cash out after gambling on the Strip will begin later this week.
Multiple casino operators on the Strip, including Caesars Entertainment, MGM Resorts International and Wynn Resorts, will only cash out poker chips from their properties, ending any preexisting arrangements for accepting poker chips from ...Read more
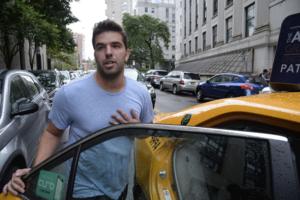
Rights to Fyre Festival sell for $245K on eBay
The rights to the troubled Fyre Festival brand have sold for only $245,000 in an eBay auction.
The sale included IP, brand trademarks and social media assets.
The auction received a total of 175 bids with the final bid coming in early Tuesday afternoon.
Organizer Billy McFarland announced he was selling the brand in April, roughly a week ...Read more
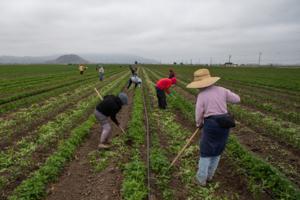
Justin Fox: A '100% American' farm workforce? That's delusional
Want a job picking fruit? There are thousands available right now on the U.S. Department of Labor’s Seasonal Jobs website. Orchard work paying $19.82 an hour in Washington, $17.96 in Pennsylvania and $15.87 in West Virginia. Berry planting and picking jobs at $19.97 an hour in California, $16.23 in Florida and $16.08 in Georgia.
Employers ...Read more
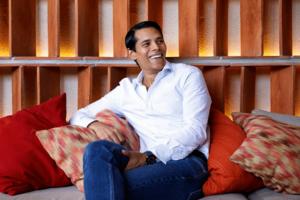
Beyond missing pets and packages: How Nextdoor plans to reshape its social network
Nextdoor, the once-hot social network for neighborhoods, wants to claw its way back to the top and prove that people can use the platform for more than just finding lost cats.
The San Francisco company's shares have plunged more than 80% since its market debut in 2021. Nextdoor shined brightly when people locked at home during the COVID-19 ...Read more
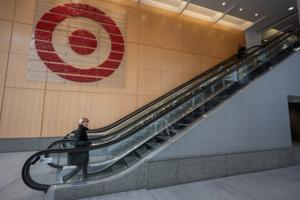
Victims of gift card scam sue Target, allege Minneapolis retailer profited from fraud
Four fraud victims who were tricked by con artists into buying Target gift cards as part of scams allege the retailer is purposefully failing to catch criminals because the company profits from selling ill-gotten merchandise.
The victims, all residents of Pennsylvania, on Monday filed a putative class-action lawsuit against Minneapolis-based ...Read more
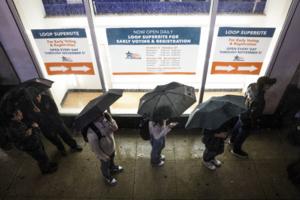
Chicago Board of Election workers should not be barred from unionizing, judge finds
The Chicago Board of Election Commissioners had previously argued that the state’s election code barred its employees from forming a union. But the law shouldn’t be read that way, administrative law Judge Anna Hamburg-Gal found in an order Monday that paves the way for official recognition of the union.
City elections workers, including ...Read more
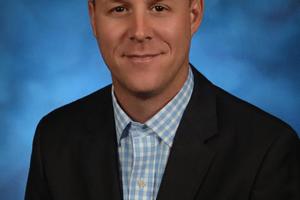
Stellantis brings back sales leader Stoicevich to work with dealers
Stellantis NV's new CEO Antonio Filosa continues to tweak his North American leadership team, with the latest move bringing back veteran sales executive Jason Stoicevich to work with regional dealers.
Stoicevich had briefly been the American sales chief last year before departing for personal reasons. After a stint as a vice president at ...Read more
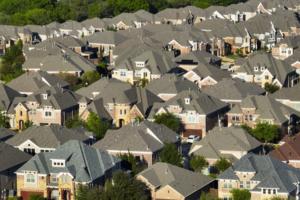
US home prices are losing steam with most big markets below peak
The U.S. housing market is close to stalling out, with prices in more than half the country’s top 100 housing markets now below their peak, according to the latest data from Intercontinental Exchange.
The annual nationwide price increase slowed to 1.3% in June, the slowest pace in two years and down from 1.6% the previous month, ICE’s ...Read more

State Farm defends hefty 27.2% hike in Illinois homeowners insurance rates
Challenged by everyone from consumer groups to Gov. JB Pritzker over its imminent 27.2% homeowners insurance rate increase in Illinois, State Farm faces the question: Will it seek to defend its widely criticized decision?
The answer: hail yes.
Citing more frequent extreme weather events such as wind, hail and tornados, insufficient premiums to...Read more
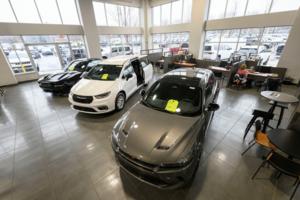
US core CPI rises less than expected again despite tariff impact
Underlying U.S. inflation rose by less than expected for a fifth month in June even as the details signaled companies are beginning to more meaningfully pass some tariff-related costs to consumers.
The consumer price index, excluding the often volatile food and energy categories, increased 0.2% from May, according to Bureau of Labor Statistics ...Read more
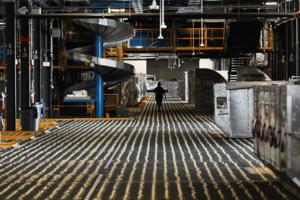
Step inside FedEx's huge new distribution hub at Detroit Metro Airport
ROMULUS, Michigan — One recent afternoon at FedEx’s new massive distribution hub, packages moved swiftly along an automated conveyor system as they were scanned, sorted, and prepped to be flown to their next destination.
The sounds of automated machinery filled the 300,000-square-foot facility — nearly twice the size of the previous ramp ...Read more
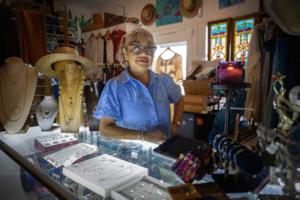
It's peak season in Malibu, but these small businesses are still struggling after the Palisades fire
LOS ANGELES — Six months after the Palisades fire roared down Pacific Coast Highway, the Country Kitchen in Malibu is open for business, but many customers have yet to return.
The no-frills eatery features a few outdoor tables and ocean views, nestled in a narrow parking lot alongside a liquor store and gift shop. The restaurant, which opened...Read more
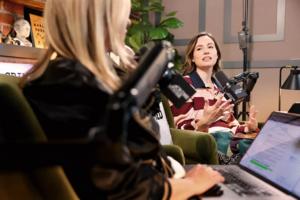
This is the rare bright spot in a tough Hollywood job market
LOS ANGELES — Toni Gray’s phone is blowing up these days.
The head of production at Dhar Mann Studios, which makes shows for YouTube and other online platforms, said entertainment industry friends in Los Angeles had once held out before seeking work in the digital realm.
But now, with jobs few and far between at the legacy studios, they ...Read more
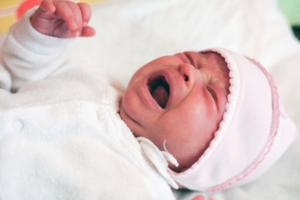
How the $1,000 'Trump accounts' for American babies compare to 529s and custodial Roth IRAs
President Donald Trump signed his new tax law on July 4, which included a provision that creates and funds investment accounts for babies born in the next few years. The accounts will be allowed to compound and grow tax-deferred, similar to the way some retirement accounts work.
“In addition to the substantial financial benefits of investing ...Read more
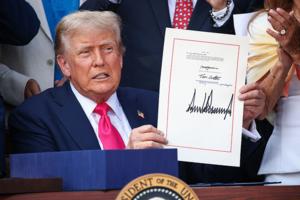
Trump's temporary tax breaks: 5 'big beautiful bill' provisions that may not stick around for long
Millions of Americans will see significant shifts in their tax bills under President Donald Trump’s “big beautiful bill.” The sweeping legislation delivers several key tax breaks, including no federal income tax on some tips and overtime pay, a car loan interest deduction, a higher state and local tax (SALT) deduction and a new “bonus”...Read more
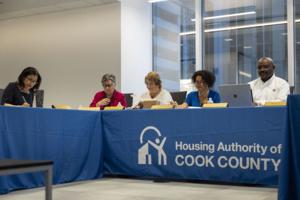
HUD Chicago office taking on more public housing authority oversight as staff dwindles regionally, nationally
The U.S. Department of Housing and Urban Development’s Chicago office will now oversee 65 public housing authorities in Wisconsin because of staffing shortages in the agency’s Milwaukee office.
This represents a roughly 62% increase in the number of public housing authorities the Chicago office is responsible for holding accountable to ...Read more
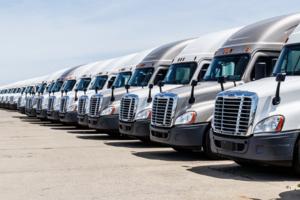
Nearly 600 Daimler Truck workers affected by layoffs in N. Carolina
Nearly 600 manufacturing Daimler Truck North America employees are temporarily losing their jobs in the Charlotte, North Carolina, region.
Daimler Truck North America is temporarily laying off 573 workers update in Gaston County, according to a N.C. Worker Adjustment and Retraining Notification Act report filed Friday with the North Carolina ...Read more
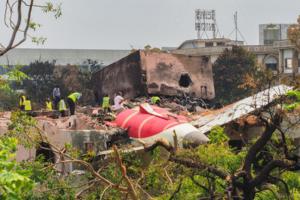
787 switches at center of Air India crash probe were scrutinized before
Boeing’s engine fuel control switches, now the center of the investigation into the fatal Air India crash in June, have been scrutinized before.
The Federal Aviation Administration warned in December 2018 that it had received reports that those switches, designed to shut down the aircraft’s engines, were installed with the locking feature ...Read more
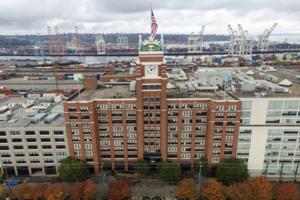
Starbucks tightens in-person work policy, offers buyouts
Starbucks will require its corporate workforce to work in the office four days a week this fall, and is offering buyouts to employees who want to leave the company.
The Seattle-based coffee giant will also force managers to relocate to corporate offices in Seattle or Toronto, ending remote options for them. Employees who aren’t managers but ...Read more
Popular Stories
- How the $1,000 'Trump accounts' for American babies compare to 529s and custodial Roth IRAs
- Step inside FedEx's huge new distribution hub at Detroit Metro Airport
- Trump's temporary tax breaks: 5 'big beautiful bill' provisions that may not stick around for long
- This is the rare bright spot in a tough Hollywood job market
- It's peak season in Malibu, but these small businesses are still struggling after the Palisades fire